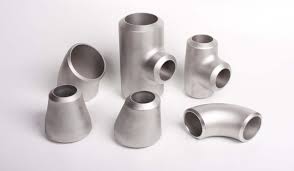
The Manufacturing Process of Buttweld Fittings: From Raw Material to Finished Product
Buttweld fittings play a crucial role in piping systems, ensuring strong, leak-proof, and durable connections for various industrial applications. The manufacturing process of buttweld fittings involves several stages, from selecting raw materials to final inspection. Understanding this process helps in ensuring the quality and reliability of these essential components. Let’s take a closer look at how buttweld fittings are made.
- Selection of Raw Material
The first step in manufacturing buttweld fittings is choosing the right raw material. Common materials include:
- Carbon steel – Used for general industrial applications due to its strength and affordability.
- Stainless steel – Ideal for corrosion-resistant applications, especially in chemical and food industries.
- Alloy steel – Used for high-temperature and high-pressure applications.
- Duplex and super duplex steel – Preferred for extreme environments requiring both strength and corrosion resistance.
The raw materials are typically in the form of seamless or welded pipes, which are carefully inspected before production.
- Cutting and Shaping
The selected pipes are cut to the required length using mechanical saws or automatic cutting machines. The shaping process varies depending on the type of fitting being manufactured:
- Elbows – Pipes are bent using a hot-forming process.
- Tees and Crosses – Pipes are split and expanded using hydraulic or mechanical presses.
- Reducers – The pipe diameter is reduced gradually through a forming process.
- Caps – The pipe end is pressed and shaped into a cap.
- Heating and Forming
After cutting, the material is heated in a furnace to a high temperature, making it more malleable for forming. The shaping of buttweld fittings is done using processes like:
- Hot Induction Bending – Pipes are heated and bent to the desired angle using induction heating.
- Die Forming – Hydraulic presses shape the pipe into different fittings like tees and reducers.
- Extrusion – The material is forced through a die to form a specific shape.
- Heat Treatment
Heat treatment is crucial for enhancing the mechanical properties of the fittings. This process involves:
- Normalizing – Heating and then cooling to refine the grain structure.
- Annealing – Heating to a specific temperature and slow cooling to improve ductility.
- Quenching and Tempering – Rapid cooling followed by reheating to enhance toughness and strength.
Heat treatment ensures the fittings meet industry standards for durability and performance.
- Machining and Trimming
Once the fittings are formed, they undergo machining to achieve precise dimensions. This includes:
- Beveling – Creating the correct weld bevel for seamless welding.
- Grinding and Polishing – Ensuring a smooth surface finish.
- Drilling (if required) – Making holes for custom applications.
- Surface Treatment and Coating
To enhance corrosion resistance and improve longevity, buttweld fittings undergo surface treatments such as:
- Pickling and Passivation – Cleaning stainless steel fittings to remove surface impurities.
- Galvanization – Applying a protective zinc coating for corrosion resistance.
- Painting or Epoxy Coating – Used for carbon steel fittings in specific applications.
- Quality Inspection and Testing
Every buttweld fitting undergoes rigorous testing to ensure it meets industry standards such as ASME, ANSI, and ASTM. Common tests include:
- Dimensional Inspection – Ensuring fittings match the required specifications.
- Hydrostatic Testing – Checking for leaks under high pressure.
- Non-Destructive Testing (NDT) – Methods like ultrasonic, radiographic, and magnetic particle testing detect internal defects.
- Chemical and Mechanical Testing – Verifying the material composition and mechanical properties.
- Marking and Packaging
Once the fittings pass all quality checks, they are marked with:
- Material grade
- Size and dimensions
- Manufacturer’s name
- Standard compliance (e.g., ASME B16.9)
Finally, the fittings are packed securely using wooden crates, plastic wrapping, or customized packaging to ensure safe transportation.
Conclusion
The manufacturing process of buttweld fittings is a complex and precise operation that ensures high-quality, durable components for industrial piping systems. From selecting raw materials to final testing and packaging, every step is crucial in producing fittings that meet industry standards. Understanding this process helps in selecting the best buttweld fittings for various applications, ensuring efficiency and safety in critical piping systems.